From Field to Fabric: How Cotton is Processed and Readied for the Market
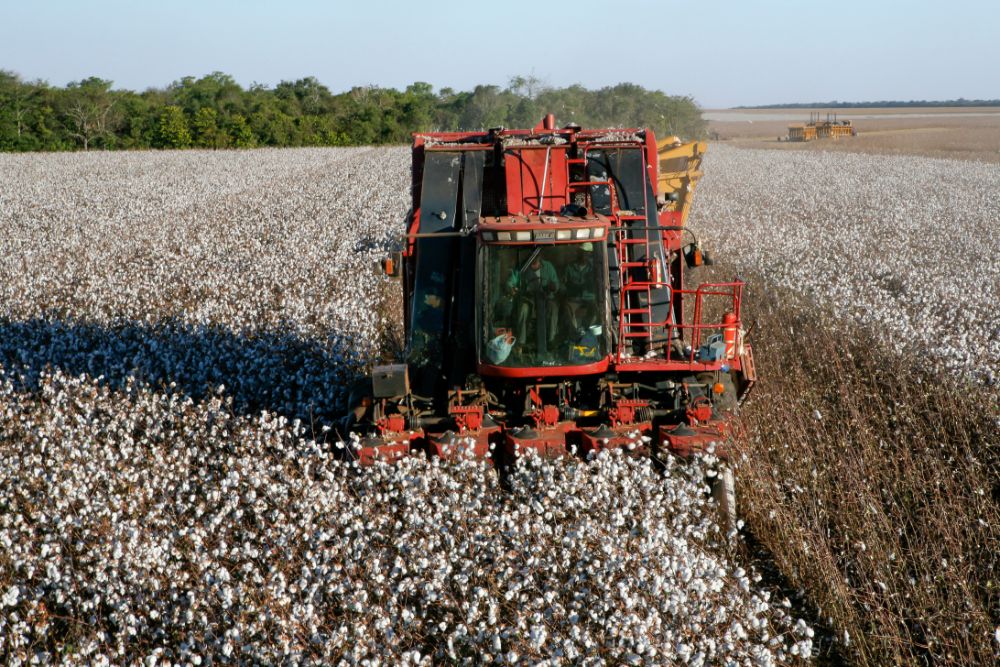
Cotton, often referred to as “white gold,” is one of the most important natural fibers used in textiles. The journey of cotton from the field to fabric is a complex, multi-step process that involves harvesting, cleaning, spinning, weaving, and finishing. Understanding how cotton is processed helps one appreciate the level of precision and effort required to make it market-ready.
1. Cultivation and Harvesting
The process begins with cultivating cotton plants in warm climates with well-drained soil. Cotton is grown primarily in the United States, India, China, and Brazil. Farmers plant cotton seeds in the spring, and the plants take about 5 to 6 months to mature.
Once the cotton plant flowers, it develops seed pods known as cotton bolls. When these bolls ripen, they burst open to reveal fluffy white fibers. At this stage, the cotton is ready to be harvested. In modern farming, mechanical harvesters, such as spindle pickers and stripper harvesters, efficiently collect the cotton while minimizing contamination. Handpicking is still practiced in some regions but is less common due to its labor-intensive nature.
2. Ginning: Separating the Fiber from the Seed
Once harvested, raw cotton undergoes ginning, which separates the fibers from the seeds and removes debris such as leaves and stems. There are two primary types of ginning:
- Saw Ginning: Circular saws pull the fibers through narrow slots, preventing seeds from passing through.
- Roller Ginning: A gentler method used for longer-staple cotton varieties, where a leather roller captures fibers, and a stationary knife blade detaches the seeds.
After ginning, the cleaned cotton fibers, known as lint, are pressed into large bales weighing approximately 500 pounds for transportation to textile mills.
3. Cleaning and Opening: Preparing the Fiber
At the textile mill, bales of cotton are loosened using machines equipped with large spikes that break apart the compacted fibers. The opened cotton passes through several cleaning stages where dirt, trash, and any remaining plant matter are removed. High-powered suction and rotating beaters further clean the cotton and separate the fibers into a soft, fluffy mass.
4. Carding: Aligning and Refining the Fibers
Carding is a crucial step in cotton processing, ensuring the fibers are aligned and free from knots and tangles. A carding machine uses fine-toothed rollers to straighten and separate the fibers, transforming them into a continuous, thin web. This web is then condensed into a rope-like strand called a sliver.
For high-quality textiles, an additional process called combing is performed. Combing removes short fibers and any remaining impurities, leaving behind longer, smoother fibers that produce stronger and finer yarn.
5. Drawing and Roving: Preparing for Spinning
The carded or combed slivers are then processed through drawing frames, where multiple slivers are combined and stretched to ensure uniformity in thickness and fiber alignment. This process enhances the consistency and strength of the final yarn.
The sliver is then converted into roving—a slightly twisted strand that is finer and more manageable for spinning. Roving adds a mild twist to the fibers, preparing them for the next step.
6. Spinning: Creating Yarn
Spinning is the process of transforming roving into yarn by drawing out and twisting the fibers. There are different spinning methods, each producing yarn with unique characteristics:
- Ring Spinning: Produces strong and fine yarn through continuous twisting and winding.
- Open-End (Rotor) Spinning: Uses centrifugal force to spin fibers into yarn, making the process faster but yielding a coarser texture.
- Air-Jet Spinning: Utilizes compressed air to twist the fibers, creating a smooth and uniform yarn.
Once spun, the yarn is wound onto cones or spools, ready for the next stage of fabric production.
7. Weaving or Knitting: Forming Fabric
Spun cotton yarn is used to construct fabric through weaving or knitting.
- Weaving interlaces two sets of yarn—the warp (lengthwise) and the weft (crosswise)—on a loom, forming a structured fabric.
- Knitting loops yarn continuously using needles, creating a stretchable and breathable fabric.
The choice between weaving and knitting depends on the intended application. Weaving is preferred for durable fabrics like denim, whereas knitting is commonly used for soft, flexible materials like t-shirts.
8. Fabric Finishing: Enhancing Quality
After fabric formation, the material undergoes several finishing processes to improve its appearance, texture, and durability. Common finishing treatments include:
- Singeing: Burns off protruding fibers for a smoother texture.
- Scouring: Removes natural oils, waxes, and impurities.
- Bleaching: Whiten fabrics for a clean base before dyeing.
- Mercerizing: Treats cotton with caustic soda to increase strength, luster, and dye absorption.
- Dyeing and Printing: Adds color or patterns to the fabric.
- Softening or Coating: Improves the fabric’s feel or functionality, such as water resistance.
Finishing ensures that the fabric meets specific quality standards before being cut and sewn into final products.
9. Quality Control: Ensuring Market-Readiness
At every stage, strict quality control measures are in place to monitor fiber length, yarn uniformity, fabric strength, and color consistency. Advanced testing equipment assesses:
- Fiber Micronaire: Determines fiber fineness and maturity.
- Tensile Strength: Measures fabric durability.
- Color Fastness: Ensures dyes remain vibrant after washing.
- Shrinkage Control: Prevents unwanted fabric shrinkage during use.
By maintaining high-quality standards, manufacturers ensure that the final product meets consumer expectations and industry regulations.
Certi-Pik, USA—Your Trusted Partner in Cotton Harvesting
From the field to fabric, cotton processing is a highly intricate operation requiring advanced machinery and technical expertise. Each step, from harvesting to fabric finishing, plays a vital role in ensuring cotton’s viability for textile production.
If you are in the agricultural industry and require high-quality replacement components for your cotton harvesting equipment, Certi-Pik, USA is your go-to source. Since 1988, we have provided durable, precision-engineered parts for top pickers in the industry. Whether you need fabricated replacement components or specialty sheet metal parts for rebuilding cotton-harvesting machines, we’ve got you covered.
Browse our range of products and ensure your cotton harvesting operations run smoothly and efficiently!