Essential Parts of a Cotton Harvester: A Detailed Guide
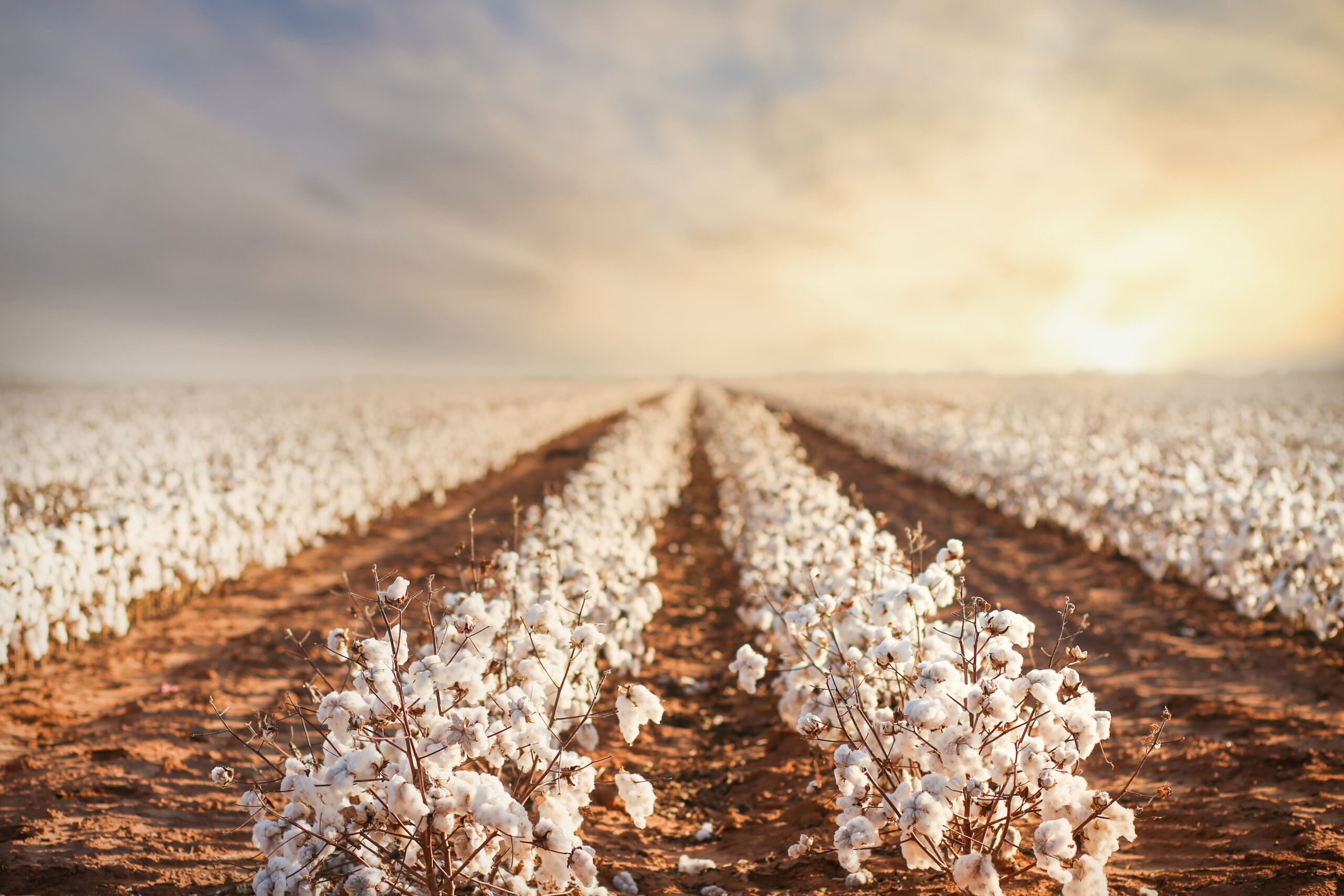
Cotton harvesting is an integral step in the cotton production process, and modern cotton harvesters have revolutionized the industry. These machines are complex, with many essential parts working in harmony to efficiently pick, clean, and store cotton. For any farmer or operator looking to maintain peak performance and longevity of their cotton harvester, understanding the individual components and their functions is critical.
Cotton Harvester Basics: How They Work
Before diving into the individual parts, it’s important to understand the general operation of a cotton harvester. There are two main types of cotton harvesters: spindle pickers and stripper harvesters. Spindle pickers are more common in the U.S. and other major cotton-producing countries. These machines utilize rotating spindles to extract cotton from the plant. Stripper harvesters, on the other hand, strip both cotton and plant material, which requires more intense cleaning processes.
Regardless of the type, the harvester’s primary function is to separate cotton fiber from the plant, process it to remove debris and store the harvested cotton for transport. Each part of the machine plays a specific role in these processes, and understanding these roles can help maintain the harvester, troubleshoot issues, and source replacement parts when necessary.
Spindles: The Core of Cotton Harvesting
Spindles are the heart of a cotton harvester. In spindle pickers, rows of spindles rotate and interact with the cotton plants. The spindles are tapered and barbed and designed to grip the cotton fibers from the open bolls without damaging the plant.
How Spindles Work:
As the harvester moves down the field, the rotating spindles brush against the cotton plants. The barbs on the spindles latch onto the cotton fibers, pulling them off the bolls. The spindles then rotate back towards the machine’s doffers, which strips the cotton from the spindle directing it into the air system and deposits it into the harvester’s storage system.
Maintenance Tip:
Due to the constant contact with the cotton plants and their high rotational speed, spindles wear down over time and must be regularly inspected and replaced when necessary. Poor spindle maintenance can lead to decreased efficiency and more fiber loss during harvesting.
Doffers: Cotton Removal from Spindles
Once the spindles have captured the cotton from the plant, the doffers play a vital role in removing it from the spindle. The doffer assembly consists of a series of urethane lugs bonded on steel discs that come into contact with the rotating spindles, scraping off the cotton fiber.
Doffer Importance:
Efficient doffing is critical to a cotton harvester’s performance. If the doffer fails to adequately remove cotton from the spindle, the machine may become clogged or experience reduced productivity. The rubbery material of the doffers also wears over time and must be adjusted or replaced regularly to maintain optimal operation.
Doffer Maintenance:
When inspecting the doffers, look for signs of wear, such as thinning rubber, cracks, or uneven surfaces. Regular replacement of doffers ensures the cotton is removed cleanly from the spindles and transferred properly to the machine’s conveyance system.
Conveyors: Moving Cotton Through the Machine
Once cotton is doffed from the spindles, it needs to be transported within the machine for processing. This is where the conveyor system comes into play. Conveyors move the cotton from the picking units to the collection baskets. In strippers a separation system further processes the picked cotton by separating debris like burs, leaves, and stems before it is deposited into the basket.
Conveyor System Types:
There are two main types of conveyor systems found in cotton harvesters:
- Air Conveyors: Use air pressure to move the cotton through tubes from the picking head to the basket.
- Auger Conveyors: Use rotating augers to physically transport the cotton.
Both systems are designed to minimize damage to the cotton and ensure a steady flow of fiber into the storage system.
Common Conveyor Issues:
Over time, the augers in belt conveyors may wear down, crack, or lose traction in their driving systems, requiring replacement. In air conveyor systems, blockages can occur if air pressure decreases, sharp corners develop from worn parts thus hanging up the cotton, or large debris enters the system, necessitating periodic cleaning to ensure proper airflow.
Harvesting Heads: Precision and Accuracy
The harvesting head is the business end of the cotton harvester, where the interaction between the machine and the cotton plant occurs. Each harvester has multiple heads, each containing spindles, doffers, and plant dividers. These heads are responsible for aligning with the rows of cotton plants and guiding them into the machine for processing.
Plant Dividers:
Plant dividers are located on the front of the harvesting heads and help guide cotton plants into the machine. These dividers are designed to avoid damage to the plants while ensuring the cotton bolls are properly positioned for the spindles to grip.
Head Height Control:
Modern cotton harvesters come equipped with sensors and automated systems that adjust the height of the harvesting heads to optimize performance. If the heads are too low, they can become clogged with soil and debris, while heads positioned too high will miss cotton bolls, reducing yield.
Cleaning System: Removing Trash and Debris
Cotton harvested by a cotton stripper is often mixed with debris such as leaves, sticks, and burs. Cotton stripper harvesters are equipped with cleaning systems to ensure clean cotton lint is stored. These systems use various techniques, such as air currents and mechanical separators, to remove as much debris as possible before the cotton is compacted for storage.
Air Cleaner:
One part of the cleaning systems is the air cleaner, which uses air pressure and gravity to filter lighter debris like leaves out of the cotton.
Rotary Screens:
Some harvesters also have rotary screens, which provide clean air for the engine to run smoothly, filtering out small particles and plant material.
Regular maintenance of these cleaning systems is crucial for optimal performance. Clogged air ducts or damaged screens can lead to lower-quality cotton being stored and less dependable machine performance, which can affect the value of the cotton crop.
Basket: Storing Harvested Cotton
The basket is where the harvested cotton is stored after it has been picked and cleaned. Modern cotton harvesters have large baskets with the capacity to store significant amounts of cotton before needing to be emptied. Some models are equipped with compaction systems that pack the cotton more tightly, allowing for more cotton to be stored in the same space.
Basket Features:
- Hydraulic Unloading: Most cotton harvesters feature hydraulic systems that lift and tilt the basket for easy unloading into a boll buggy or module builder. Baler machines use hydraulics to raise the rear of the machine to allow the bale to come out and be deposited on the ground.
- Compaction Systems: These systems, weather producing a round or square bale, compress the cotton to maximize storage capacity, reducing the number of times the basket needs to be emptied.
Regular inspection of the basket and its components ensures smooth unloading and prevents downtime in the field.
Drum Assemblies and Sheet Metal Components
Drum assemblies and various sheet metal components are essential in guiding the cotton through the machine. These components provide structural support and help direct cotton into the proper channels for cleaning and storage.
Over time, these parts can wear out due to constant exposure to plant material, dirt, and moisture. Keeping an eye on the condition of drum assemblies and sheet metal parts is essential for preventing breakdowns.
Sheet Metal Maintenance:
Corrosion and wear are the main concerns for sheet metal components. Regular cleaning and inspection can extend the life of these parts, but replacement is often necessary to maintain the integrity of the machine. Keeping adequate pressure on service doors is important to keep debris from wedging in unwanted areas potentially bending the doors.
Hydraulic Systems: Powering the Harvester
Hydraulic systems play a pivotal role in powering various functions of the cotton harvester, from controlling the height of the harvesting heads to operating the unloading mechanism for the basket. Hydraulics ensure the smooth operation of heavy components, making them indispensable for modern machines.
Hydraulic Maintenance:
Keeping hydraulic fluid at the appropriate level and ensuring there are no leaks is critical for the longevity of the system. Faulty hydraulics can lead to slower operation or complete shutdown of key components, so staying vigilant about their upkeep is essential.
Engine and Drive System: Moving the Machine
Finally, the engine and drive system are what keep the cotton harvester moving through the field. Cotton harvesters are large machines that require powerful engines to navigate the terrain while simultaneously powering the various mechanical and hydraulic systems.
Drive System Components:
- Transmission: Transfers power from the engine to the wheels or tracks of the harvester.
- Wheels/Tracks: Many modern cotton harvesters are equipped with tracks instead of traditional wheels, which improve their ability to navigate uneven or muddy terrain.
Proper maintenance of the engine, transmission, and drive system ensures that the cotton harvester remains operational throughout the season. Regular oil changes, inspections, and repairs help prevent costly downtime.
Keeping Your Cotton Harvester in Top Shape
Maintaining a cotton harvester requires knowledge of its essential parts and understanding how each component contributes to the machine’s overall performance. From the spindles that pick the cotton to the hydraulic systems that power the machine, regular maintenance and timely replacement of worn-out parts are crucial to maximizing efficiency and minimizing downtime.
When you’re looking for a company that can provide quality-made replacement parts for your cotton harvester, look no further than Certi-Pik, USA. Since 1988, we’ve been working with customers from around the world, providing fabricated replacement components for top pickers in the industry. We also offer a full range of specialty items and customized components to help you rebuild and maintain your cotton-harvesting equipment. For high-quality parts and exceptional service, Certi-Pik, USA is your trusted partner in cotton harvesting.