How John Deere Harvesters Are Changing Cotton Harvesting Practices Worldwide
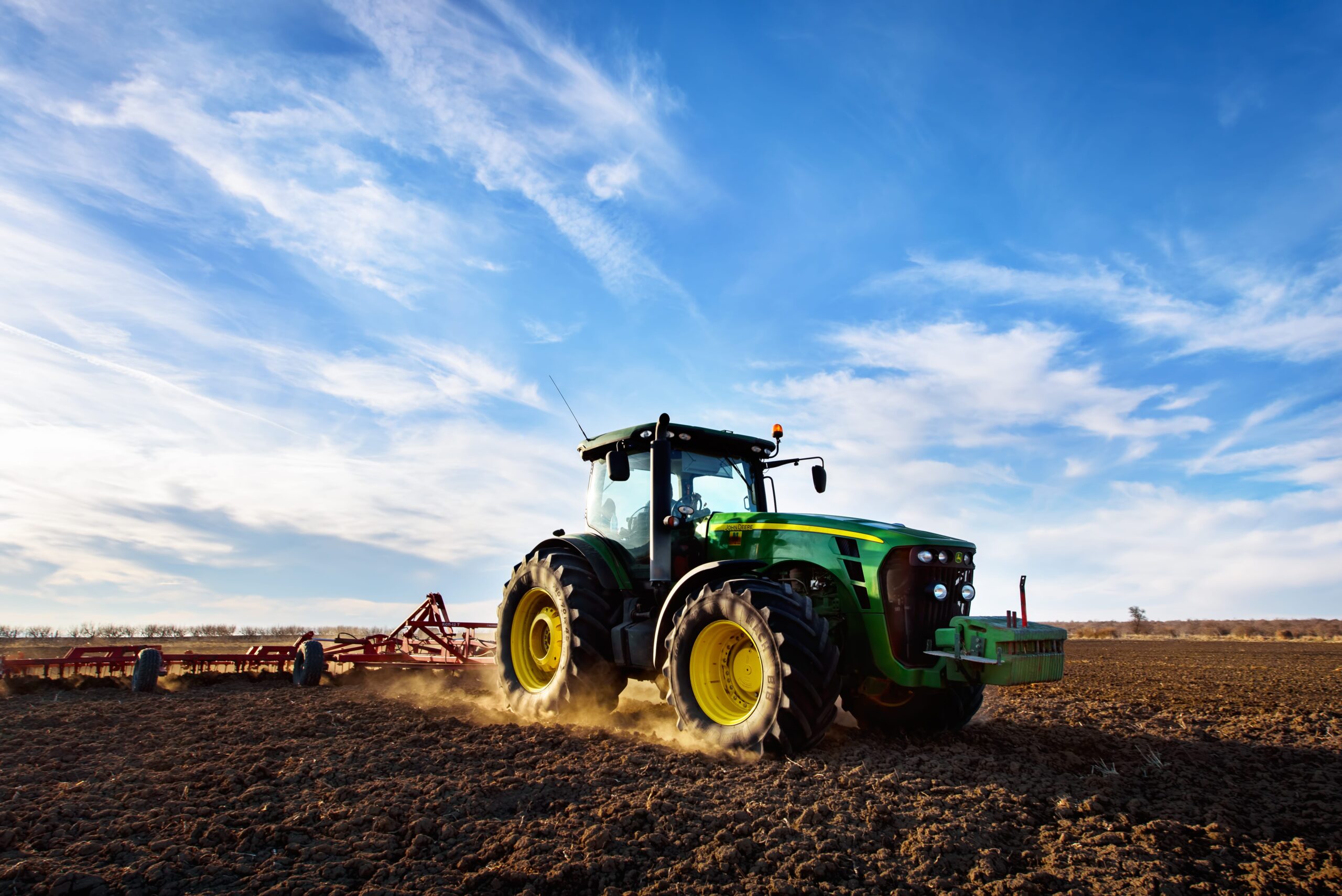
Cotton harvesting is one of the most labor- and machine-intensive agricultural operations, requiring precision, speed, and durability from every piece of equipment involved. Over the years, John Deere harvesters have stood at the forefront of innovation in this sector. These machines have played a significant role in transforming how cotton is picked, processed, and prepared for market—not just in the United States but around the globe.
The Evolution of Cotton Harvesting Machinery
Before mechanization, cotton was picked by hand—a backbreaking and time-consuming process. The introduction of mechanical cotton pickers in the 20th century revolutionized the industry. Initially, these machines were cumbersome, prone to breakdowns, and required multiple passes through the field to achieve a full harvest.
John Deere entered the cotton picker market with equipment designed for higher reliability, ease of use, and operational efficiency. Through decades of engineering improvements, their harvesters have become some of the most respected and widely used machines in global cotton production.
From conventional basket-style cotton pickers to the advanced round module-building machines we see today, John Deere harvesters have driven massive gains in productivity and consistency in cotton harvesting.
Transitioning from Basket Pickers to Onboard Module Builders
One of John Deere’s most significant technological shifts was the development of onboard module builders. Traditional basket-style pickers required separate boll buggies and module builders at the edge of the field. This setup necessitated additional labor, fuel, and time to transport cotton from the field to the module builder.
In 2007, John Deere launched the 7760 Cotton Picker, the first commercial onboard round module builder. This development meant that cotton could be picked, compacted, and wrapped in plastic in a continuous, in-field operation. Not only did this drastically reduce the need for additional support equipment, but it also minimized fiber contamination and exposure to the elements.
The ability to produce consistent, wrapped modules directly in the field has changed the game for growers in regions with unpredictable weather patterns. It reduces crop exposure to rain and dew and allows cotton to be ginned more efficiently due to standardized module size and shape.
Key Technical Features of Modern John Deere Harvesters
John Deere harvesters incorporate a wide range of advanced features that boost field efficiency, reduce downtime, and ensure cleaner cotton collection. Some of the most notable technical enhancements include:
1. ProDrive™ Transmission System
This hydrostatic transmission system offers infinite speed adjustment and automatic shifting between high and low ranges. It ensures maximum ground speed during harvesting and allows the operator to maintain consistent picking speed across variable field conditions.
2. Round Module Wrap System
Modern John Deere harvesters, such as the CP770 and CS770, include integrated systems for producing round cotton modules wrapped in plastic film. These wraps not only protect the cotton from weather and contamination but also feature embedded RFID technology for tracking and logistics.
3. Cab and Operator Controls
John Deere has prioritized operator comfort and usability in their harvesters. The cab is pressurized and climate-controlled, with intuitive touchscreen displays for monitoring machine functions, adjusting picking unit settings, and tracking yield in real-time.
4. RowSense™ and AutoTrac™ Guidance
These GPS-enabled systems allow for hands-free steering along the rows, reducing fatigue and increasing accuracy in both single-pass and multi-pass harvesting. The result is reduced overlap, fewer missed plants, and greater overall efficiency.
5. High-Capacity Picking Units
John Deere’s spindle-type picking units are engineered to provide gentle yet effective cotton removal with minimal plant damage. Each unit is equipped with moistening systems, rotating doffers, and spindles that efficiently grasp and twist off cotton fibers.
Impact on Harvest Efficiency and Labor
One of the most important benefits of modern John Deere harvesters is the reduction in labor requirements. Historically, a cotton harvest operation required a small fleet of equipment and a team of operators—pickers, boll buggy drivers, module builder operators, and support personnel.
With the advent of onboard module building, much of this labor has been consolidated. A single machine can now perform the work of three or four older systems. This is especially beneficial in countries facing labor shortages or high operational costs.
The increase in harvester efficiency also means that growers can harvest larger acreages in shorter time frames. This is critical in regions where harvesting windows are narrow due to weather, pest pressure, or regulatory limits.
Global Adoption of John Deere Harvesters
While originally engineered for U.S. row crop conditions, John Deere harvesters have found widespread adoption in cotton-producing nations around the world, including:
- Australia: Australian cotton farms, known for their scale and mechanization, rely heavily on the latest John Deere harvesters. The climate and geography demand machines that can perform long hours with minimal downtime.
- Brazil and Argentina: South American growers appreciate the harvester’s ability to navigate hilly terrain and variable field conditions while maintaining module uniformity.
- India and Pakistan: In regions where cotton is still partially handpicked, John Deere is working with local partners to adapt their machines for smaller field sizes and different crop varieties.
- Africa: As mechanization grows in sub-Saharan Africa, John Deere harvesters are being used to help modernize cotton production in countries like Burkina Faso and Zambia.
John Deere’s global dealer network, training support, and parts availability have played a crucial role in this international growth.
Sustainability and Cotton Quality Improvements
In addition to enhancing efficiency, John Deere harvesters contribute to more sustainable cotton farming practices. By reducing the number of trips across the field and consolidating operations into a single pass, these machines lower fuel consumption and minimize soil compaction.
Furthermore, the use of plastic-wrapped round modules helps to maintain cotton quality by preventing moisture contamination. Cleaner cotton translates to higher ginning efficiency and better market pricing.
Newer harvesters are also equipped with yield monitoring technology, which gives growers detailed insights into plant performance across their fields. These insights allow for more targeted fertilization and irrigation, improving sustainability over time.
Maintenance and Replacement Parts: The Hidden Backbone of Performance
While the technological advancements of John Deere harvesters have been widely praised, they also require a high level of mechanical reliability to perform under intense field conditions. Spindle assemblies, moistener pads, picker bars, cam tracks, drumheads, and other wear parts are constantly exposed to stress, friction, and contamination.
Keeping a harvester in optimal working condition means having access to precision-fabricated replacement components. Growers and repair shops worldwide rely on aftermarket parts suppliers to meet this critical demand.
For those who operate or maintain John Deere harvesters, working with a trusted parts manufacturer is essential to minimizing downtime and maximizing machine lifespan. Whether rebuilding a major assembly or replacing worn metal sheets, precision is key.
Certi-Pik, USA: Your Trusted Source for Harvester Replacement Parts
When your John Deere cotton picker needs quality replacement parts, you don’t want to take chances with subpar components or extended lead times. That’s where Certi-Pik, USA comes in.
At Certi-Pik, USA, we specialize in fabricated replacement parts for John Deere cotton-harvesting equipment. Since 1988, we’ve been delivering high-performance components to customers across the U.S. and around the globe. Our product lineup includes everything from sheet metal picker panels to specialty items and hard-to-find rebuild components.
Here’s what sets Certi-Pik, USA apart:
- Precision Engineering: Every part is manufactured to exacting tolerances, ensuring proper fit, function, and durability.
- Comprehensive Inventory: We carry a wide selection of parts compatible with many John Deere models, including legacy machines and the latest harvesters.
- Worldwide Shipping: We can deliver the parts you need quickly and reliably no matter where your operation is located.
- Experienced Support: Our team understands harvester systems inside and out. We’re here to help you find the right parts and keep your machines running smoothly.
Whether you’re a commercial cotton grower, a regional repair shop, or a distributor serving multiple clients, Certi-Pik, USA is your go-to resource for dependable replacement parts.
The Future of Cotton Harvesting Starts Now
John Deere harvesters have redefined cotton harvesting by delivering more automation, better efficiency, and improved cotton quality. From integrated module builders to GPS-guided precision systems, these machines are setting new global standards.
However, even the best machines require ongoing maintenance and access to quality replacement parts. If you operate a John Deere cotton picker and need replacement components that match or exceed OEM standards, look no further than Certi-Pik, USA.
For over 35 years, we’ve been helping customers rebuild, maintain, and optimize their cotton-harvesting equipment. With a comprehensive inventory, technical expertise, and commitment to quality, we’re proud to be the partner that keeps your operation running.
When you’re looking for a company that can sell you a quality-made replacement part for your harvester, look no further than Certi-Pik, USA. We’ve been working with customers from around the world since 1988, providing them with fabricated replacement components for the top pickers in the industry. We also sell a full range of specialty items and sheet metal components for use in rebuilding cotton-harvesting equipment.