What Are the Essential Parts of a Cotton Harvester?
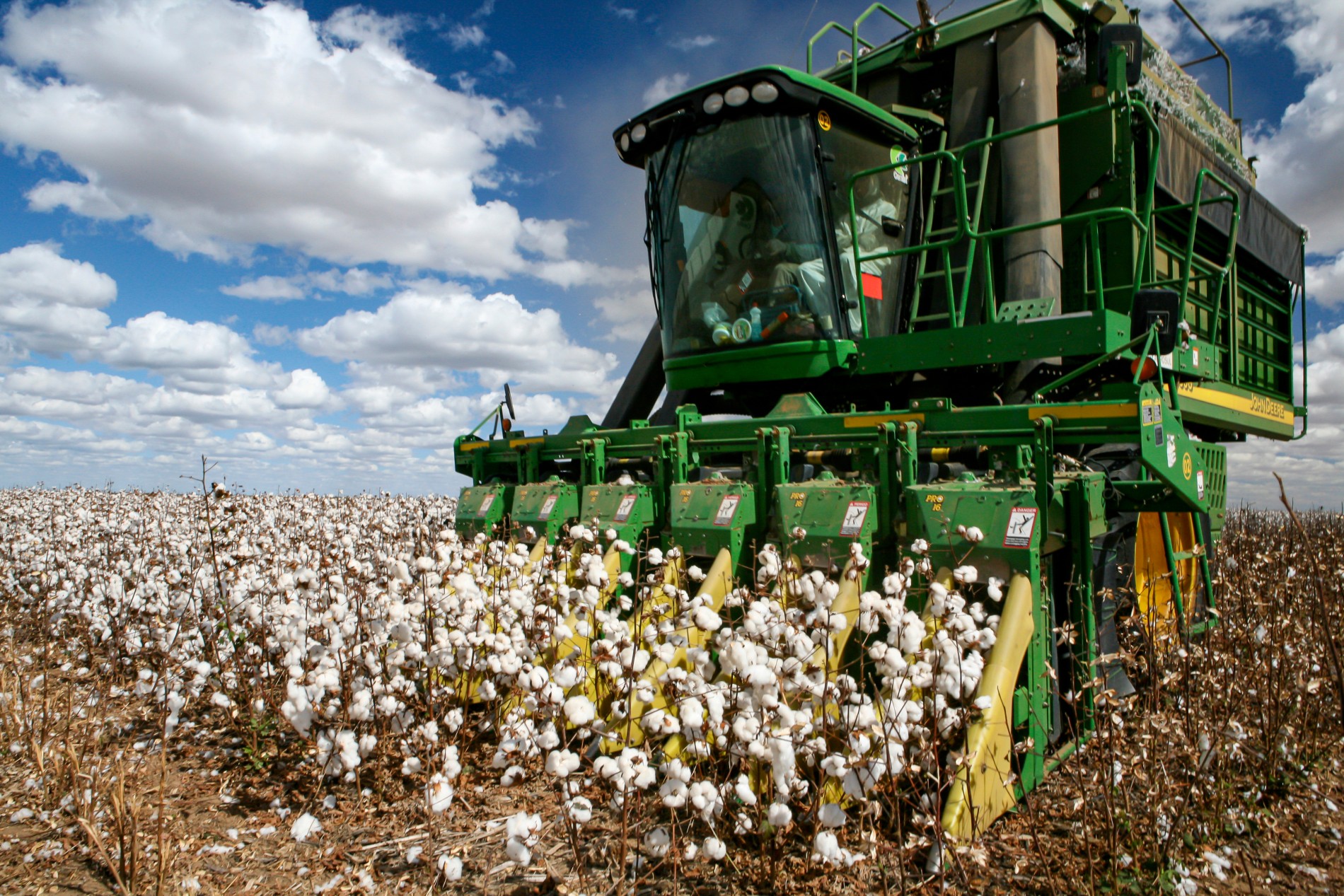
Cotton harvesting is a critical process in the agricultural industry, requiring state-of-the-art machinery to ensure efficient and effective crop collection. The cotton harvester, a marvel of agricultural engineering, is a machine designed to reap this essential crop while minimizing waste and maximizing efficiency. However, for the uninitiated, the components that make up these complex machines can seem overwhelming.
Introduction to Cotton Harvesters
Before diving into the nitty-gritty of its components, it’s crucial to understand what a cotton harvester is. A cotton harvester, often called a cotton picker or machine, is specialized agricultural equipment designed to harvest cotton plants. These machines come in two primary types: the picker type, which removes the cotton fibers from the bolls without damaging the plant, and the stripper type, which removes the entire boll along with the cotton fiber in addition to a portion of the woody plant. Each type has its specific components, but some parts are common to both mainly outside of the picking units.
Essential Parts of a Cotton Harvester
Engine and Powertrain
Any heavy-duty agricultural machine starts with a robust engine that provides the necessary power to perform its tasks efficiently. The engine in a cotton harvester often ranges in horsepower depending on the machine’s size and capacity. It drives not just the machine but also powers the numerous hydraulic systems within. Alongside the engine, the powertrain components, including the transmission and differentials, work together to manage and distribute this power to the harvester’s various functions, such as the picking units and the transport system.
Picking Units
The picking units are the heart of a cotton harvester. Depending on whether the harvester is a picker or stripper type, they are available in different forms.
Spindles (For Picker Type)
In a picker-type cotton harvester, the picking units include numerous rotating spindles. These spindles are thin, barbed rods that penetrate the cotton bolls and twist, entangling the fibers around them. The high-speed rotation of their sharp barbs allows them to pluck the cotton from the plant without significant damage.
Doffers and Moistener Pads (For Picker Type)
Once the spindles catch the cotton, the cotton must be removed and transferred to a collection area. Doffers perform this task. Doffers spin the opposite direction as the spindle to strip the cotton off the spindles’ barbs. The spindles then pass under the moistener pads’ flexible fins to clean the sticky cotton oils from the spindles.
Stripper Rolls (For Stripper Type)
Stripper-type harvesters use different mechanisms. Stripper rolls hold a series of bats and brushes. Rubber-bats and nylon brushes are used to strip the entire boll from the plant, and often much of the plant itself. Using fewer bats per roll can reduce the amount of foreign material or the woody plant fibers that contaminate the cotton. These rolls rotate at high speed, ensuring they collect as much cotton as possible often from shorter plant varieties or matted-wet cotton fibers.
Conveyor Systems
Once the cotton fibers are collected, they must be transported efficiently to the machine’s storage section. Conveyor systems handle this task.
Air Conveyors
Cotton picker harvesters use air conveyors to move the cotton from the picking units to the holding chambers on the pickers. These pneumatic systems utilize a venturi effect using suction airflow to transport the cotton fibers, reducing mechanical wear and improving efficiency.
Auger Conveyors
In cotton strippers, a header auger conveys the cotton to the air system which sends the cotton into the basket. In newer strippers, an onboard field cleaner separates lighter cleaner cotton from heavier picked cotton and contaminants. The heavier product drops out and is processed through a series of spinning blades and grid bars where the lighter cotton is again sucked away from the heavier trash and sent to the basket. The remaining unwanted foreign material is discharged out of the machine to the ground.
Storage Basket
The storage basket, also called a boll basket, is where the harvested cotton is temporarily stored before it gets transported for ginning. This containment area is either a basket on older machines or a chamber where the cotton is compressed into a bale on newer harvesters.
Capacity and Compaction
The storage basket’s capacity can significantly affect harvesting operations’ efficiency. Modern baskets often come with compaction mechanisms, which press the cotton into a round or square bale to make room for more, allowing the harvester to operate longer before needing to unload.
Hydraulic System
The hydraulic system in a cotton harvester is extensive and multifaceted. It controls the various moving parts of the machine, including lifting and lowering the basket, steering, and operating the picking units.
Hydraulic Pumps and Motors
Hydraulic pumps provide the necessary fluid pressure, which is converted into mechanical force by hydraulic motors that drive different components. This system enables smooth, controllable motion critical for the precision needed in cotton harvesting.
Electronics and Control Systems
Modern cotton machines are equipped with sophisticated electronics and control systems to enhance efficiency and precision.
GPS and Auto-Steering
Global Positioning Systems (GPS) and auto-steering technologies are increasingly common. These systems help in precision farming by ensuring optimal path planning, reducing overlaps, and covering maximum area with minimal waste of time and resources.
Monitoring Sensors
A range of sensors monitor various aspects of the harvesting process, from spindle speeds to cotton flow rates and hydraulic pressures. These sensors feed data into a central control unit, which processes the information and adjusts real-time machine settings.
Cab and Operator Controls
The cab of a cotton harvester is designed for operator comfort and efficiency. Given that operators often work for extended periods, features such as climate control, ergonomic seating, and intuitive control panels are paramount.
Control Panels and Displays
The control panels typically feature touchscreen displays providing vital information regarding the harvester’s status. Operators can make real-time adjustments to the picking units, conveyor systems, and other components directly from these panels.
Maintenance and Accessibility Features
Accessibility for maintenance is a critical aspect that is often overlooked but of great importance. The easier it is to access and maintain various parts of the machine, the less downtime one experiences due to repairs or servicing.
Access Panels and Diagnostic Ports
Access panels allow easy entry to critical components for routine maintenance and debris removal. Diagnostic ports offer a quick and effective way to hook up electronic diagnostic tools, speeding up troubleshooting processes and minimizing downtime.
Tires and Tracks
Tires or tracks facilitate the mobility of the cotton harvester. Given the challenging nature of cotton fields, the choice between tires or tracks can significantly impact the machine’s performance.
Tires
Tires are more common and offer the benefit of faster movement along paved roads and more straightforward replacement. They also provide a good balance between traction and ground pressure.
Tracks
Tracks offer superior traction and stability, particularly in uneven or wet fields. They distribute the machine’s weight more evenly, reducing soil compaction—a crucial factor for maintaining field health.
The Importance of Quality Parts
Understanding the essential parts of a cotton harvester underscores its complexity and sophistication. Each component plays a vital role in ensuring efficient and effective cotton harvesting. However, the performance and longevity of these components are as good as their quality. Inferior parts can lead to frequent breakdowns, lower efficiency, and increased operational costs.
Replacement Parts and Rebuilds
When your cotton harvester needs a replacement part or you’re looking to assemble the components necessary for a rebuild, it’s crucial to use parts that match or exceed the original equipment manufacturer’s (OEM) standards. High-quality replacements not only extend the life of your machine but also contribute to better overall performance.
Contact Us Today
If you need replacement parts for your cotton harvester or are planning a rebuild, consider reaching out to Certi-Pik, USA. We provide an extensive range of replacement parts produced by our rigorously held standards. Our expertise and commitment to quality ensure that you get the best components for your cotton machine, enhancing its efficiency and longevity.
Don’t let inferior parts slow down your operations. Trust Certi-Pik, USA for all your cotton harvester needs. Contact us today and keep your harvest running smoothly and efficiently.