The Role of the Cotton Picker Spindle: Why Quality Matters in Harvest Efficiency
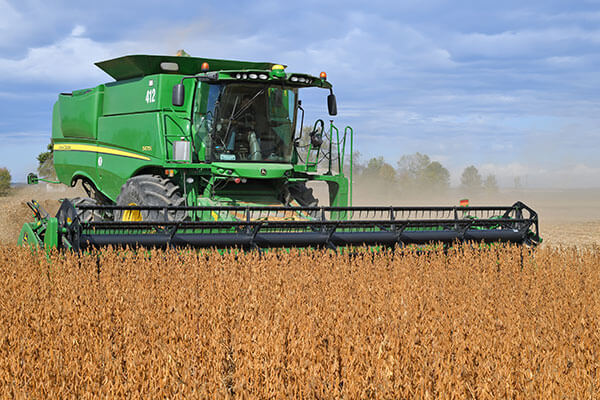
The cotton industry depends on machinery that can reliably perform in rugged field conditions while delivering high yields with minimal fiber damage. One of the most critical components in this process is the cotton picker spindle. These rotating components do the essential job of extracting cotton from the plant’s bolls. Though small compared to other parts of the harvester, the spindle plays an integral role in determining the efficiency, productivity, and profitability of each harvest.
Understanding the function, wear factors, and importance of spindle quality is vital for anyone operating or maintaining a cotton picker.
What Is a Cotton Picker Spindle?
A cotton picker spindle is a slender, barbed shaft that rotates at high speeds to pull cotton fibers from the open bolls as the machine passes through the field. Spindles are threaded into picker bars, arranged in drum assemblies. They are lubricated though the picker bar with grease and cleaned by the moistening systems to maintain picking effectiveness and reduce plant contamination.
The barbs on the spindle catch and hold the cotton, which is then removed by doffers and conveyed into the machine’s basket for storage. The spindle’s design and sharpness determine its ability to grip the cotton fibers while minimizing harm to the plant and lint.
Modern cotton pickers may utilize hundreds of spindles per row unit. That means a multi-row picker can operate thousands of spindles simultaneously, making their maintenance and quality critical for optimal harvesting.
The Role of the Spindle in Harvest Efficiency
Cotton harvesting is a time-sensitive process. Factors such as crop maturity, weather windows, and equipment availability all come into play. Since the spindle is the component that physically removes the cotton from the plant, its performance directly affects:
- Harvest speed
- Fiber retention
- Plant damage
- Lint quality
- Field cleanliness
A worn or poorly manufactured spindle may break fibers, leave cotton behind on the plant, or cause more contamination from leaf and plant matter. On the other hand, a sharp, properly aligned, and high-quality spindle enables the picker to collect more cotton faster and with less strain on the entire system.
Key Performance Metrics for Cotton Picker Spindles
When evaluating cotton picker spindles, several technical performance characteristics must be considered:
- Sharpness and Wear Resistance: A good spindle maintains sharp barbs that pierce and wrap the cotton fiber effectively. Worn barbs reduce picking efficiency.
- Barb Geometry: The angle, spacing, and shape of the barbs influence how well the cotton is captured and held during extraction.
- Gear Geometry: Head Height and Minimal runout on the gear teeth ensure smooth function and optimal operating backlash and clearances.
- Material Composition: Spindles made from hardened steel and adequate chrome coated alloys resist abrasion and corrosion better.
- Straightness and Balance: Properly manufactured spindles must maintain precise tolerances to prevent vibration, misalignment, and wear on other components.
- Lubrication Compatibility: Spindles should be compatible with the picker’s lubrication and cleaning system to maintain performance and reduce heat buildup.
Common Causes of Spindle Wear and Damage
Cotton picker spindles operate in harsh environments, including exposure to dirt, plant debris, and variable field conditions. These factors can accelerate wear and lead to premature failure. Common causes of spindle degradation include:
- Normal abrasive wear from plant material and cotton fibers
- Inadequate or contaminated lubrication
- Corrosion from moisture or chemical residues
- Improper installation or alignment
- Use of incompatible or inferior not approved aftermarket parts
Operators should conduct regular inspections and maintenance checks, focusing on spindle wear patterns, broken spindles, and barb sharpness. Even a single damaged spindle can affect adjacent components and reduce overall harvesting quality.
How Poor-Quality Spindles Affect the Entire Harvest Operation
Choosing subpar spindles to save costs can backfire in several ways:
- Increased Downtime: Low-quality spindles are more prone to bending or breakage, misalignment, or premature wear, leading to more frequent repairs and downtime.
- Higher Operating Costs: Inferior spindles can increase fuel consumption, wear on drive systems, and the need for more frequent part replacements.
- Reduced Yield: Cotton left on the plant due to poor spindle performance represents lost revenue.
- Decreased Fiber Quality: Broken or damaged fibers lower the grade and value of the harvested cotton.
- Component Wear: Misaligned or unbalanced spindles can damage other components, such as doffers, moistener pads, and bushings, leading to compound repair issues.
Benefits of Using High-Quality Replacement Spindles
Replacing worn or damaged spindles with high-quality replacements ensures that your cotton picker continues to operate at peak performance. Some of the advantages include:
- Extended Equipment Lifespan: Quality parts reduce wear on adjacent components.
- Improved Harvest Speed: Sharp and well-formed barbs capture more cotton in less time.
- Higher Yields: Efficient picking results in less cotton left behind.
- Better Fiber Integrity: Clean extraction maintains the natural strength and color of the fiber.
- Reduced Maintenance: Fewer breakdowns and consistent performance reduce total maintenance hours.
When every second counts during harvest, the reliability of your spindles can make or break your schedule and profitability.
Factors to Consider When Choosing a Replacement Cotton Picker Spindle
There are several critical factors to evaluate when selecting replacement spindles for your cotton harvester:
- OEM Compatibility: Ensure the spindle matches the make and model of your picker.
- Precision Fabrication: Look for spindles manufactured to tight tolerances for straightness and balance.
- Surface Treatment: Hardened and chromed spindles resist wear and corrosion.
- Vendor Reputation: Source parts from trusted suppliers with experience in the industry.
- Availability and Support: Timely delivery and technical support are essential, especially during harvest season.
Certi-Pik, USA is known for delivering fabricated components that meet or exceed OEM standards. It offers spindles designed for top-brand pickers.
Complementary Components that Work with the Cotton Picker Spindle
While the spindle is the core of the cotton-picking mechanism, it works in tandem with other components to deliver optimal results. These include:
- Doffers: These remove cotton from the spindles and play a key role in maintaining clean extraction.
- Bushings and Bearings: These support the rotational motion of the spindle and reduce friction.
- Spindle Moistening Systems: Keep spindles clean and lubricated, enhancing picking performance.
- Picker Bars and Drum Assemblies: House the spindles and ensure synchronized motion across the unit.
Maintaining these related components is just as important. Damage or wear in one area can compromise the entire picking system.
Maintenance Best Practices for Cotton Picker Spindles
Preventive maintenance ensures longer spindle life and consistent harvesting. Best practices include:
- Daily inspections of spindles and picking units during harvest season
- Routine replacement of worn spindles
- Monitoring spindle moistener system performance
- Checking for misalignment or wobble
- Greasing bearings and ensuring proper lubrication
Proactive spindle care reduces emergency repairs and maintains high harvesting standards throughout the season.
Trust Certi-Pik, USA for Reliable Cotton Picker Spindles
When it comes to maximizing your harvest efficiency, the quality of your cotton picker spindle cannot be overlooked. This small but vital component has a direct impact on yield, fiber quality, and machine durability. Ensuring that your picker is equipped with high-performance spindles is an investment in your entire operation.
At Certi-Pik, USA, we understand the demands of cotton harvesting. That’s why we furnish replacement spindles and other critical components with unmatched attention to detail. We’ve been working with customers from around the world since 1988, providing them with dependable parts for the top pickers in the industry.
In addition to spindles, we sell a full range of specialty items and sheet metal components for rebuilding cotton-harvesting equipment. Our reputation is built on precision, quality, and commitment to customer satisfaction.
When you’re looking for a company that can sell you a quality-made replacement part for your harvester, look no further than Certi-Pik, USA. Contact us today to learn more about our spindle options and how we can help keep your harvest running smoothly.